Uncertainty surrounding tariffs and trade policies is making it difficult for businesses to plan and manage their supply chains effectively. Businesses can adapt by diversifying suppliers, rerouting their supply chains, and adopting technology to help them mitigate the impact of tariffs.
Governments worldwide have been weighing a variety of tariffs and retaliatory measures. Some of these duties have already gone into effect, others are on the negotiating table, and more are likely to be announced. This article takes a close look at the implications for company supply chains.
What Are Tariffs?
Tariffs are taxes that companies pay on goods imported from other countries. Tit-for-tat disputes between trading nations mean that tariffs can negatively impact businesses in two ways:
- Imports: Tariffs imposed by a company’s home country on imported raw materials, components, and finished products raise the prices the company must pay for those goods.
- Exports: Tariffs imposed by foreign countries often compel companies that export to those countries to raise prices on those goods to compensate, making themselves less competitive in those markets.
8 Implications of Tariffs on the Supply Chain
Tariffs have historically been used to prop up domestic industries or protect them against subsidized foreign competitors. By increasing the price of imported goods, governments seek to encourage citizens to buy homemade products instead. However, this kind of industrial policy can result in higher prices for both domestically produced and imported goods, as well as retaliatory tariffs from governments abroad. Recently, governments has also used tariffs as leverage in negotiations on issues other than trade, such as border control, causing greater uncertainty.
Whether they’re used for industrial policy or political leverage, tariffs can contribute to a government’s treasury. For example, such duties accounted for about 1.6% of US federal revenue in 2024. The average duty across all US imports hit a low of 1.2% in 2008, rising to 2.8% by 2022, according to the most recent comparable data, with individual tariffs rising as high as triple-digit percentages based on type of product and country of origin.
Tariffs represent only one of the many financial and logistical factors impacting companies’ supply chains. Other challenges include international logistics, currency fluctuations, overseas sales taxes (such as Europe’s value-added taxes), and official trade barriers (such as subsidies and customs procedures). Focusing on tariffs, the implications for supply chains include:
- Business uncertainty: With so many trade routes subject to tariff changes that may or may not last, it’s hard for companies to navigate around the problem. As one expert put it: “Where do you go?” Restructuring a company’s sourcing and production is costly, complex, and time-consuming. For example, in capital-intensive industries, such as manufacturing, companies must plan months—even years—in advance to complete the required investments.
- Shifts in sourcing: Mexico overtook China as the United States’ biggest trading partner in 2023, reflecting US companies’ decisions to nearshore their production and sourcing closer to home. More recently, though, Mexico has faced potentially large US tariffs that could undermine the value proposition of that nearshoring. Such shifts are occurring in other countries, too.Experts recommend at least two strategies near term. One is to gradually diversify suppliers and production centers to serve different regional markets, despite the negative implications for economies of scale and supplier relationship management. Another is to invest in better software to manage procurement, inventory management, and supply chain processes, often through the implementation of an enterprise resource planning (ERP) system—to improve operational efficiency and agility. Notably, however, everything from raw materials and components to specialized skills and adequate infrastructure may be hard to find in new places.
- Increased costs: Tariffs raise the cost of imported raw materials, components, and finished products. Though a company may negotiate with its suppliers to share the cost burden, much of this expense is ultimately passed on to customers in the form of higher prices. Some businesses have already invested in tariff mitigation strategies to strengthen their supply chains against abrupt changes in trade policies. They’ve diversified geographic locations, stockpiled inventory, and adjusted pricing and cost absorption methods, according to the International Chamber of Commerce (ICC). But these adaptations can be costly and reduce profitability while providing no fail-safe against further trade disruptions.
- Decreased export competitiveness: When a national government increases tariffs, domestic companies can face a double whammy. Their production costs can increase, due to the higher prices they must pay for imported raw materials and components. And if foreign governments retaliate with tariffs of their own, those same companies may find it harder to compete when exporting to the foreign countries.
- Inventory challenges: Facing impending and unpredictable tariffs, some companies have been stockpiling imported goods before the tariffs take effect. The National Retail Federation reported the busiest December on record for US imports. But the association cautioned that stockpiling imported inventory increases costs for warehousing and is known to strain cash flow, tying up money needed for operations, debt repayment, investment, and other essentials.
- Trade retaliation: When a country imposes tariffs on its trading partners, those partners often retaliate with tariffs of their own, a cycle that can escalate, leading to trade wars and geopolitical tension.
- Encouragement of domestic production: Part of many countries’ trade strategy is to encourage domestic companies to source and manufacture more goods locally rather than import from overseas. Reshoring may offer companies some operational and cost benefits at a time when wages, trade barriers, and shipping delays are increasing in countries abroad. Reshoring is typically considered as part of a broader supply chain restructuring, with companies strategically placing different parts of their supply chains in various national, regional, and overseas locations.
- Bureaucratic burden: Complying with tariffs and other trade regulations adds administrative complexity to supply chains, encouraging companies to elevate their global trade management skills. Global trade management software can help companies weigh different sourcing options based on landed costs that incorporate tariffs on top of product prices and shipping expenses. Such software can also automate customs reporting. Notably, many companies seek exemptions from tariffs, which is another complex, bureaucratic process.
Mitigate Risk to Your Supply Chain With NetSuite
NetSuite can help companies navigate today’s volatile trade environment. NetSuite ERP and supply chain management software give companies the visibility needed to understand costs associated with tariffs and their impact on the business. For example, staff can run a profit analysis of each import with a landed costs feature that breaks out tariffs and other expenses. AI capabilities help businesses run scenarios on alternative suppliers, products, and costs to find the best options, as well as help them evaluate the potential impacts of absorbing cost increases or passing them on to customers. Companies can also use the software to analyze their supply chain operations to find efficiencies that might offset at least part of the cost of new tariffs.
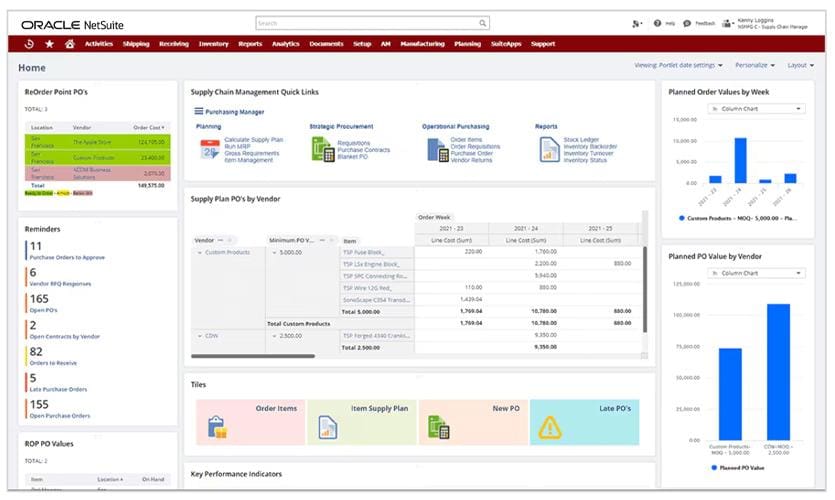
The outlook for international trade is clouded by heightened geopolitical tensions, as major trading nations exchange tit-for-tat tariffs and retaliatory measures. As the International Chamber of Commerce points out, companies urgently need predictability and certainty to plan investments, manage supply chains, and operate effectively in global markets. Amid the uncertainty, businesses can take steps to analyze their options, streamline their operations, and plan for multiple scenarios to maintain supply chain resilience.
#1 Cloud ERP
Software
Implications of Tariffs on the Supply Chain FAQs
What is an example of a tariff?
One example of a tariff is the 10% levy the United States recently imposed on all Chinese imports, prompting China to respond with tariffs on certain US goods.
What does a tariff do to supply?
As tariffs rise, increasing the price of goods imported from abroad, affected companies often seek alternative, lower-cost suppliers.