Manufacturers often hesitate to upgrade their ERP systems due to fears of disruption and complexity, but by proactively addressing risks such as business disruption, system dependency, compliance, and costs, they can successfully transition to more efficient systems.
5 Ways to Avoid Risk When Moving on to a New ERP
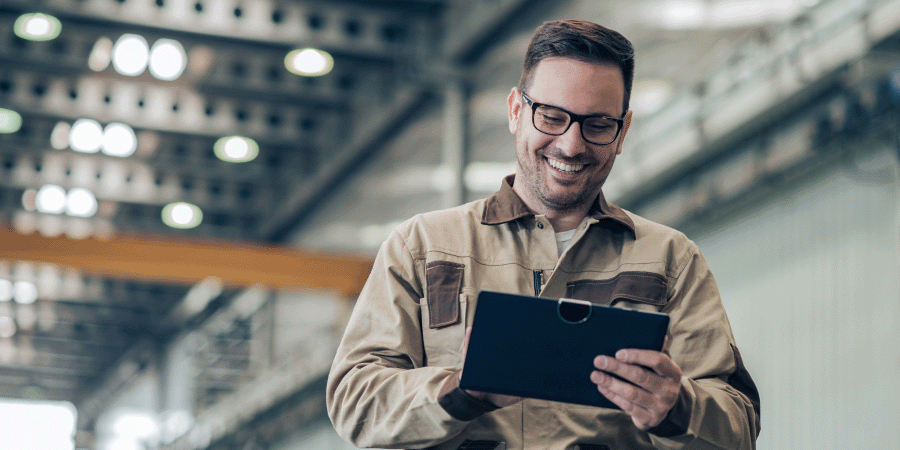
Key Takeaways
⇨
Manufacturers often delay ERP upgrades due to fears of change, but doing so can lead to inefficiencies and strategic setbacks.
⇨
To minimize business disruption during ERP implementation, use a phased approach, parallel systems, and thorough staff training.
⇨
Address common risks such as system complexity and regulatory compliance by assembling experienced teams, conducting needs assessments, and selecting reliable vendors.
YOU MIGHT ALSO LIKE